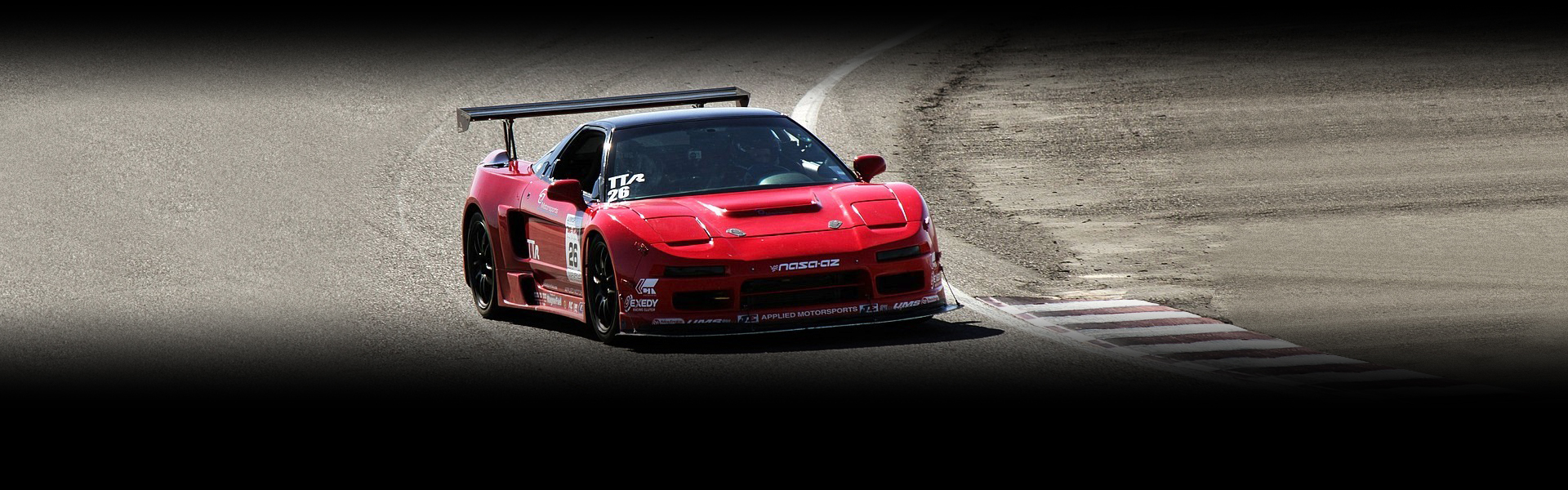
No Water – No Problems
Water – great for drinking but not ideal for engine cooling.
First used in engines some 100 years ago, water-based coolants are universally acknowledged to have inherent physical and chemical limitations that effect long-term reliability, increase maintenance costs and often restrict engine performance.
Statistics published by manufacturers and motoring organizations confirm, that water is the root cause for 60% of engine breakdowns and 40% of catastrophic failures. While internal damage goes mostly unnoticed in new engines, the cumulative effects of corrosion, cavitation and cyclic pressurization become increasingly apparent over time.
For decades engine designers and antifreeze formulators have persisted with water while endeavoring to overcome its intrinsic shortcomings – primarily because there has been no viable alternative. Over the last twenty years Evans waterless engine coolants have been tested and proven by OEM’s, fleet operators, racing teams, professional restorers, plant operators and automotive aficionados to increase reliability and reduce operating costs. The high boiling point of Evans Coolants are also facilitating improvements in engine design, performance and fuel economy.
- Water-based coolants need to be drained and replenished every 1 to 4 years, because the corrosion inhibitors breakdown* over time (*depletion by oxygen and galvanic activity). Evans has been proven to last the life of the engine, without needing replacement or requiring additives.
- The effectiveness of water-based coolants are subject to their quality, metal compatibility and regular renewal. If the coolant quality is poor (cheap), incompatible or not renewed regularly then corrosion (via oxidation and galvanic activity) will quickly take hold and damage/failure is inevitable. Evans does not oxidise inside an engine or support galvanic activity, effectively preventing water caused corrosion.
- Water freezes at 0ºC and so water-based coolants must contain sufficient antifreeze (usually 50% Toxic Ethylene Glycol) to prevent freezing in winter. If the antifreeze concentration has been depleted or diluted over time then major freeze damage can occur. Evans has natural antifreeze properties freezing below -40ºF, does not degrade and is Less Toxic. Thus eliminating the worry about topping-up or recharging with antifreeze every winter.
- Water turns in to steam at 100ºC. Mixing ethylene glycol antifreeze with water (50-50) increases the boiling point to 102.778ºC. Fitting a pressurized cap can raise system pressure and thus the coolant boiling point. A typical 1 Bar (14.5psi) pressure-cap theoretically raises the boiling point of 50-50 coolant to 122.778ºC, which you would expect to be sufficient to prevent boiling. In reality pressure drops within the cooling system, combined with very high metal temperatures adjacent to the combustion zone often result in boiling coolant and the formation of steam-vapor pockets. Steam is a poor heat transfer medium and localized overheating is often the cause of pre-ignition, detonation, increased fuel consumption and reduced power delivery. Once a steam-vapor pocket is formed it will not readily condense and can lead to full-overheat, piston-liner scuffing, cylinder-head warping and eventually total engine failure.
- Evans has a boiling point above 190.556ºC which ensures it will not boil or turn to vapor inside an engine. By remaining as a liquid under all engine loads effective heat transfer is maintained. Water-based coolants turn to steam-vapor where there is sufficient temperature combined with a drop in pressure. The rapid formation of vapor bubbles inside a liquid is better known as Cavitation. If the local pressure increases rapidly the vapor bubble will collapse with significant force, enough in fact to erode metal. The process of rapid cavitation and bubble collapse adjacent to engine liners is a common cause of erosion – sometimes to the point of catastrophic liner failure. Because car engines liners are usually cast within the main block it is impossible to see if cavitation-erosion is occurring. However large diesel engines are fitted with removable (wet) liners, which are often replaced due to severe erosion – in the form of deep pitting. In an attempt to reduce wet-liner pitting additional nitrite and nitrate inhibitors are added to heavy-duty coolants. A similar form of cavitation-erosion can occur inside pump chambers (volutes) and the associated impellers. Pump and impeller erosion results in reduced coolant flow rates and an increase in overheating.
- Evans coolants have a much lower vapor pressure compared with water-based coolants, which means they are far less prone to cavitation or causing cavitation-erosion. In a John Deere cavitation test at Southwest Research Institute in San Antonio, Texas, Evans reduced liner pitting by 70% in comparison to the next best coolant tested.
- Water generates high vapor pressures as its temperature increases – approx 1 Bar (14.5psi) at 100˚C. These pressures exert internal stress on all cooling system components, especially hoses, pump seals and radiator seams. When the engine cools the pressure reduces. i.e. the process is cyclical and repetitive, which often leads to fatigue and component failure.
- Evans coolants generate much lower vapor pressure in comparison to water – so low in fact that it is possible to remove the radiator or expansion bottle cap whilst the engine is running. This pressure reduction eliminates internal stress on hoses, pump seals and radiator seams, thus extending operating life by many years and preventing breakdowns.